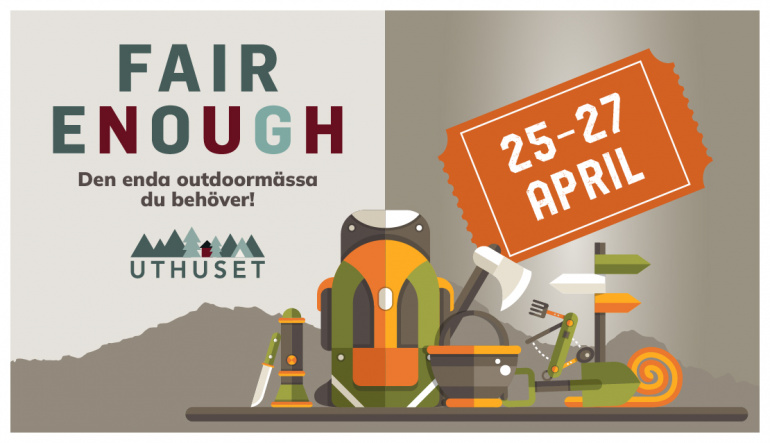
Uthuset Allehanda
Western Mountaineering från insidan
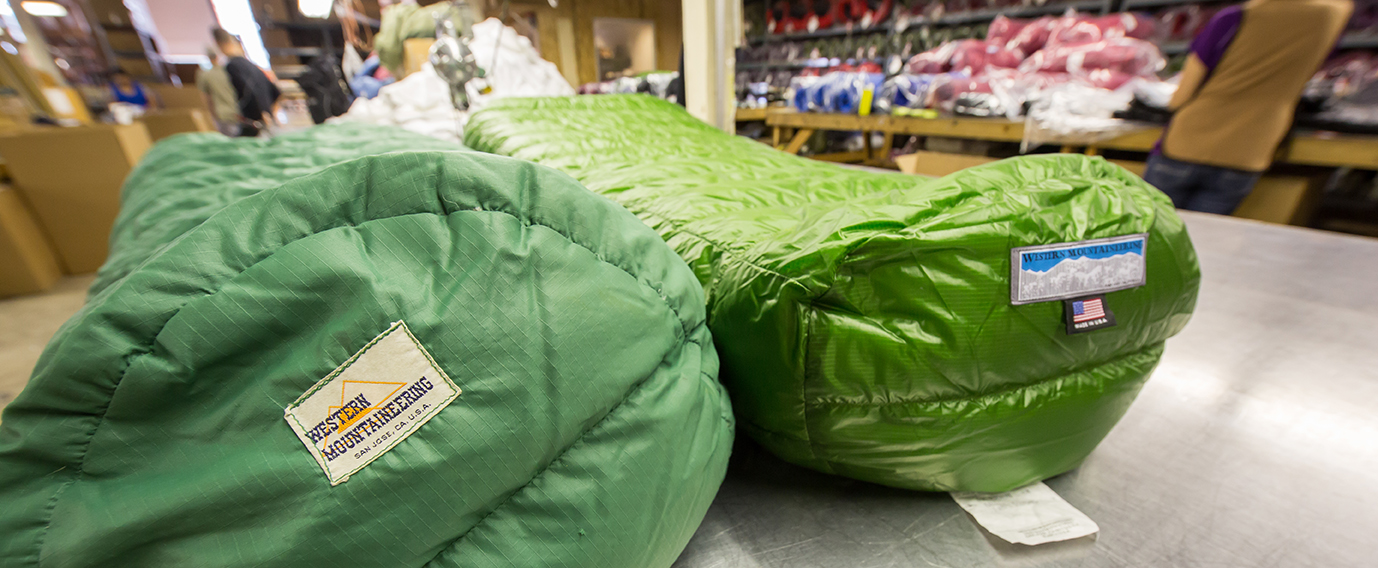
The great relationship with Uthuset
Hi Folks! My name is Gary Peterson and I have been the managing director at Western Mountaineering since for at least two and a half decades. In 1992 I spent over 200 days of my last year in college climbing then returning home for tests or to turn papers in and work to save up for the next trip. A close friend and climbing partner who used to be a production manager at Western Mountaineering asked me if I wanted to join him on a trip to Africa. I agreed and began working at Western Mountaineering in addition to waiting tables so that I could save up for the trip. Right away I learned that none of the management staff or supervisors spoke Spanish, yet that was the primary language of all but two of our sewing staff. Being fluent in Spanish and English I began translating questions and clearing up issues with our sewing machine operators just days after starting. I also had many questions about the fabrics and materials we used that couldn’t be answered right away. In searching for these answers I began taking on more responsibilities, eventually moving on to ordering raw materials and designing products.In the summer of 2003 I met Jocke Sundberg in Friedrichshafen, Germany at the Outdoor show and he wanted to sell our products at a store he had opened in Bodafors Sweden. We were very excited to work with Jocke and he became the first and only dealer in Sweden for our products until many years later. Since then we have become good friends and I have also had the pleasure of meeting and working with Kajsa. I have visited both of them on a number of trips to Sweden and we have also spent time together at trade shows in Germany and in the USA for close to two decades. Jocke and Kajsa have spent so much time with me learning about how we manufacture everything that they are the most knowledgeable source of information for Western Mountaineering products in Sweden and perhaps all of Scandinavia. I am so glad they have given me the opportunity to share some history with the outdoor enthusiasts of Sweden. The company has been around for over 50 years but I will start with a brief introduction to the Western Mountaineering brand.
Sedan tidigt 2000-tal har vi jobbat med Western Mountaineering.
About the Western Mountaineering brand
Nestled in the heart of Silicon Valley is a small sewing factory that has been manufacturing high quality sleeping bags since 1970. Now surrounded by some of the world’s most successful tech companies, the San Jose, California factory of Western Mountaineering continues churning out world class down sleeping bags in an early 1900’s warehouse. The factory building, once a coca cola bottling plant, sits within a 30km radius of Google, Apple, Tesla, and countless other Silicon Valley giants (Netflix, Paypal, Adobe, etc.). Today it seems like a strange place to manufacture sleeping bags, but in the early seventies many outdoor brands emerged from California including North Face, Patagonia, Marmot, & Sierra Designs. Most of the other brands shifted their production to other countries, outsourcing the manufacturing processes to sewing contractors in other countries like China, Vietnam, Taiwan, Cambodia, and other places with lower taxes, fewer regulations, and (most importantly) cheap labor. What makes us unique is that we are one of the only companies still manufacturing every sleeping bag in California.Over the years we have been approached by so many offshore factories wanting to produce down sleeping bags for us, but we have never wanted to trust the production process to a contractor. They all say that their quality will match ours. Perhaps it could be possible, but so far I have been vastly underwhelmed with the quality or consistency of the finished down bags coming out of contract factories for other brands. It is not that we have better sewing machine operators in California, we just do things very differently. For example only two people responsible for sewing any given sleeping bag. Most big factories split the sewing process into 30 or more small functions and they pay everyone piece rate wages to do each small task. One person is just sewing Velcro tabs on while another is sewing labels all day and so on. Every task is divided up and spread out to dozens of workers and they push through huge production runs for one brand before moving onto another set of products from a different brand. From our perspective, we think it is better to have fewer more carefully trained specialists sewing each sleeping bag.
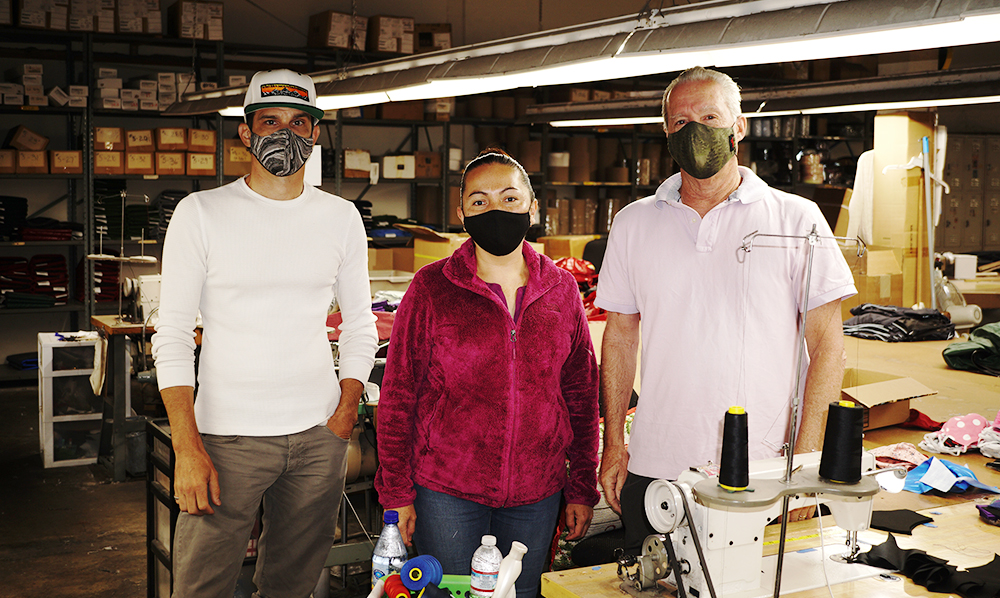
Gary P. Jackie S. och Gary S. i egensydda munskydd.
Our manufacturing process is more detail oriented and we spend twice as much time on every sleeping bag than an offshore factory but that is why our bags last such a long time. Some factories have opened up the seams to look inside our products and asked us why we double stitched and overlocked certain parts of the bag. Some of them would even laugh and say it takes too long to do that and it can’t be seen anyways. Also hot cutting of all the raw edges on the small parts must take forever, they say. We know, but all of these things make the product last longer so that is why we do it. This is why we have never outsourced the manufacturing process on our sleeping bags to an offshore contractor. At the moment our biggest challenges are with shipping delays on raw materials due to unusually heavy port congestion and, oddly enough, the weed business in California. Ever since they legalized pot here it has been harder to find sewing machine operators. People with sewing experience would rather trim buds for $25 an hour and get paid in cash daily rather than sew for $18 or $20 an hour and get a check every two weeks.